AGCがプロセスの最適化で目指すサステナブルな苛性ソーダ濃縮システム
AGCは、千葉工場の苛性ソーダの濃縮工程における蒸発器1台およびエコノマイザー4台の計5台を、アルファ・ラバル専用設計の蒸発缶およびガスケットプレート式熱交換器に交換した結果、蒸気使用量を約10%削減、大型循環ポンプの停止による電力使用量削減、機器の省スペース化を実現しました。また、ガスケット交換頻度を減らすことで生産計画に対する影響の最小化およびメンテナンス費用の削減も見込んでいます。
更新日 2025-04-02AGCは、千葉工場の苛性ソーダの濃縮工程における蒸発器1台およびエコノマイザー4台の計5台を、アルファ・ラバル専用設計の蒸発缶およびガスケットプレート式熱交換器に交換した結果、蒸気使用量を約10%削減、大型循環ポンプの停止による電力使用量削減、機器の省スペース化を実現しました。また、ガスケット交換頻度を減らすことで生産計画に対する影響の最小化およびメンテナンス費用の削減も見込んでいます。
脱炭素化に向けた化学品製造のチャレンジ
脱炭素社会の実現に向けて新エネルギーや新素材へ注目が集まる一方で、多くの産業の根幹を担う化学品製造事業においても、環境負荷を低減するために製造プロセスをいかに効率化するかが大きな課題となっています。
世界最大級のガラスメーカーであるAGCは、ガラスの原料の一つであるソーダ灰の製造技術を源流とした化学品事業を展開しています。主力製品の一つである苛性ソーダは、品質向上・環境負荷低減・省エネといった時代のニーズに合わせてその製法を転換させてきました。
AGC化学品カンパニーの使命である「私たちは化学の力を通じて安全、安心、快適で環境に優しい世の中を創造します」の下で、より高効率で安全な製造プロセスを構築することで、「産業のコメ」とも呼ばれる苛性ソーダを世の中に安定供給することが、人々の快適な暮らしを守るために重要であると考えています。そのためにも、いかにプラントの稼働率を上げるか、トラブルを最小限に抑えるかが重要です。
- 岡田俊介氏 AGC株式会社 千葉工場化学品部電解課 プロセスエンジニア(取材当時)
「苛性ソーダの濃縮工程には3つの大きな課題がありました。1つ目は老朽化した既設のシェル&チューブ式蒸発器のメンテナンスに大きな費用がかかっていたこと、2つ目は苛性ソーダの電解プラントは大量のエネルギーを消費するため、サステナビリティ目標に向けてプロセス設計を見直すことでエネルギー消費量を削減する必要があったこと、3つ目は濃縮工程に設置されていた既設のプレート式熱交換器のガスケットを、漏れのリスクから頻繁に交換しなければならなかったことでした」とプロセス基本設計を担当していた姜 唯宇氏は当時の状況を振り返ります。
「高温・高濃度の苛性ソーダを取り扱う濃縮工程の設備は特に過酷な環境下で稼働しています。万が一漏れが発生してしまうと大きな事故につながる可能性があり、長期の稼働停止を招く恐れがあります。「安全なくして生産なし」の精神から、安全設計が特に求められるプロセスであると考えています。AGC化学品カンパニーは、基礎化学品からフッ素系の高機能素材、ライフサイエンス製品までを一貫したプロセスで生産する「ケミカルチェーン」を基盤としており、その起点となる苛性ソーダプラントの稼働停止は広範囲にわたって非常に大きい影響を及ぼします。」
プロセス改善によるエネルギー効率化
AGCがこの課題を解決するために選んだソリューションが、アルファ・ラバルのガスケットプレート式熱交換器と新開発のガスケット「HeatSeal(TM)」です。このガスケットにはAGCが開発したフッ素ゴムである「AFLAS 600X」が使われており、従来のガスケットと比較して耐熱性や耐酸化性が大幅に向上していて、200℃までの連続運転に対応可能です。「この材料は樹脂とゴムの中間体のような性質を持っていて、耐強酸性、耐アルカリ性、耐熱性が特長です。耐アルカリ性を活かして、耐アミン性が要求されるガスケットプレート式熱交換器でも使用可能であることは、従来のフッ素ゴムとは大きく異なる強みであり、その差別化技術を元に半導体、電線用途に留まらず、海外では資源掘削といった特殊な部品向けで使われています」と化学品開発部の河合剛氏は述べています。
AGCの海外工場では、既に旧タイプのAFLASによるガスケットを用いたアルファ・ラバルのプレート式熱交換器の実績がありました。同社で電解プラントの設備管理を担当する吉川拓弥氏は、「導入に際しては、ガスケット耐久性の向上、機器の小型化および工事やメンテナンスのしやすさについては実績もあるのでもちろん期待をしていました。ポンプは従来比で1/20以上に小型化でき、ポンプの電気代削減だけでも大きな効果が実現できました。加えて、アルファ・ラバルの蒸発・濃縮プロセスのスペシャリストであるTomas Kovacsが、どのようにプロセスを見直せばエネルギー効率化を実現できるか、という段階から当社が持っていない知見をもってサポートをしてくれました」と語っています。
更なる可能性
姜氏は今後の展開について、「電解プロセスは約50年の歴史があり、成熟したプロセスです。省エネ化の取り組みにおいて、今回の濃縮工程の改造では年間数千万円のエネルギー消費量削減が実現できましたが、他のテーマでは同様の規模のインパクトは一度で達成することは困難です。
またプロセスが最適化されるにつれ、プラントの運転条件は過酷になってきます。プロセスに適合した長期的に安定なガスケットは本プラントの共通課題であり、今回のHeatSealA導入の取り組みは世界中のAGCグループに情報共有されており、今後は他拠点でも導入検討が進んでいくと思います。千葉工場においては、既設でまだ残っているシェル&チューブ式熱交換器の更新のタイミングで、高効率化・省スペース・メンテナンス費用削減のためにアルファ・ラバルのガスケットプレート式熱交換器に変更していきたいと考えています」と述べています。「エネルギー効率化はもちろん、メンテナンスコスト削減も大きく見込んでいます。タイトなスケジュールで点検・交換を終えるために、アルファ・ラバルの効率的なサービスに期待をしています。」
※取材当時の情報に基づいて作成されました。
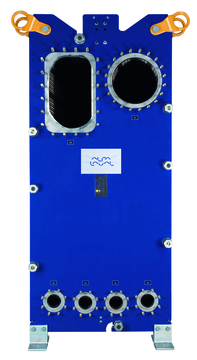
導入機種
- AlfaVap 650 (nickel) 1基
- TL10P (nickel with HeatSealTM gaskets) 2基
- TL10B (nickel with HeatSealTM gaskets) 2基
省エネ化
蒸気の使用量を10%削減、大型ポンプの停止も合わせた大幅な電力消費量を削減
稼働率向上
ガスケット交換頻度の低減による稼働停止やメンテナンスコストを削減
プレート式の採用
シェルアンドチューブ式からガスケットプレート式熱交換器+HeatSeal(TM)へ切り替え
ダウンロード | 事例・関連資料PDF
下記フォーム入力より本事例のPDFデータをダウンロードいただけます。
* フォームは英語になっておりますが、お名前・会社名は日本語でご記入ください。