Energy balance - Heat recovery at Finnish pulp mill
In the pulp and paper industry, recovery of secondary heat can mean big savings – something the Finland-based UPM-Kymmene Group knows firsthand.
DATE 2023-11-28 AUTHORPapermaking requires huge amounts of energy to maintain the heating and cooling processes the industry requires. Finland-based UPM-Kymmene, Europe’s biggest forest industry group and one of the world’s largest paper manufacturers, has fine-tuned the balance between heating and cooling processes, resulting in surplus energy.
Heat recovery from warm water is most profitable if the pulp and paper mills form an integrated whole – as in Kaukas, where heat recovery at the pulp mill saves steam for use in the paper mill.
Process integration is key to cooling warm water flows in pulp mill processes, without the need for condensing towers, resulting in energy savings and improved energy economics.
The Kaukas pulp mill is part of UPM-Kymmene’s facilities (comprising two paper mills and the pulp mill) at Kaukas, near the Finnish city of Lappeenranta, close to the Russian border. Together the Kaukas facilities produce 590,000 tons lwc (lightweight coated) paper annually and 720,000 tons of bleached sulphate pulp.
Energy self-sufficiency
UPM-Kymmene has been working toward energy self-sufficiency for the past 10 years. The Kaukas pulp mill underwent a large extension and modernization program at the end of the 90s and is since then considered energy self-sufficient – a goal achieved by recovering secondary heat from cooling processes for reuse elsewhere in the plant. Asko Paakki, operations manager of Kaukas Pulp Mill, estimates that between 10 and 20 percent of energy recovered at the mill is used elsewhere on the site. “The energy surplus is sold, usually in the form of process steam to the paper and especially the saw mills,” he says.
“Energy recycling requires intricate planning and a holistic approach”
Such recycling requires intricate planning and a holistic approach to cooling needs and recovery possibilities throughout the entire plant.
It is a balancing act. Secondary heat – by definition heat transferred from primary heat sources to process flows – is recovered in cooling and condensation waters, using a system of heat exchangers, and recycled through the plant. More than 100 heat exchangers transfer secondary heat from where it is not required to where it is required, creating an energy balance in the mill that saves Kaukas millions of euros in energy costs each year.
Industry trend
The trend in the pulp and paper industry is to develop processes toward effluent-free operation to reduce wastewater flows and to improve process efficiency. This means higher wastewater temperatures which require additional cooling, explains Pekka Svinhufvud, manager of energy economics at UPM-Kymmene’s Kaukas Pulp Mill.
Svinhufvud says the energy-saving possibilities of process integration are very plant-specific. “They depend on the process concept, the mill layout and the energy and water balance of the plant. Paakki explains that process effluent must be cooled from 70 to 80 degrees Celsius (158 to 178 degrees Fahrenheit) to below 40° C (104° F) before it goes to the biological effluent treatment plant, because the micro-organisms will not survive higher temperatures. At Kaukas, this heat is recovered using natural water in a heat exchanger – an alternative to the cooling towers used in many pulp and paper mills, where heat is simply released into the atmosphere.
In the pulp mill, cooling water from the evaporation plant, filtrates from the bleaching plant, hot water from cooling and warm water from the gas flue scrubber have the most potential for heat recovery.
“When we commenced our cooperation, testing and trials were conducted with a couple of Alfa Laval heat exchangers. After two years of satisfactory results, we bought more and more. We are continuously looking for opportunities to recover heat. We are still changing the manufacturing process and are now looking at an area between inter-filtrate exchange.” - Asko Paakki, operations manager of Kaukas Pulp Mill
Heat exchangers at core of heat recovery
A completely new heat recovery system with WideGap plate heat exchangers redesigned to gain higher temperatures has been installed at the UPM-Kymmene Kaukas Mill in Finland to allow recovery of secondary heat with Alfa Laval as the main supplier. Alfa Laval also redesigned 13 spiral heat exchangers to increase efficiency.
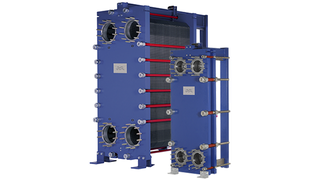
About WideGap
Alfa Laval developed WideGap plate heat exchangers especially for the pulp and paper and sugar industries, for the cooling of effluent containing fibres and other components. With the wide gaps between the plates, the plate pattern and the smooth port design allowing fibres and particles to flow easily, clogging is minimized and uptime maximized.
Thanks to its counter-current flow a WideGap can heat the cold stream to a temperature very close to that of the entering hot stream, maximizing energy recovery. Heat sources Alfa Laval WideGap plate heat exchangers can be utilized that were previously seen as waste heat. As a result, live steam consumption can be reduced, and excess steam can be used for electricity production.
Energy savings
Millions of euros saved every year through the recovery of secondary heat.
Technology shift
Switch from shell-and-tube heat exchangers to WideGap plate heat exchangers, because of their ability to recover heat.