Battery value chain
The need for batteries is growing rapidly due to the global shift towards renewable energy and electric vehicles (EVs). According to the International Energy Agency (IEA), batteries are crucial for achieving commitments made by nearly 200 countries to triple global renewable energy capacity by 2030. Additionally, the demand for EV batteries is expected to rise sevenfold by 2030.
The battery value chain involves refining raw materials like lithium and cobalt into battery-grade materials, followed by the production of cathode active materials (CAM) used in battery cells. These cells are then assembled into battery packs for EVs and energy storage. At the end of their life, batteries are collected and can be recycled to recover valuable materials for reuse, ensuring a sustainable supply of critical materials. Continuous innovation in each stage is essential to enhance efficiency and reduce environmental impact.
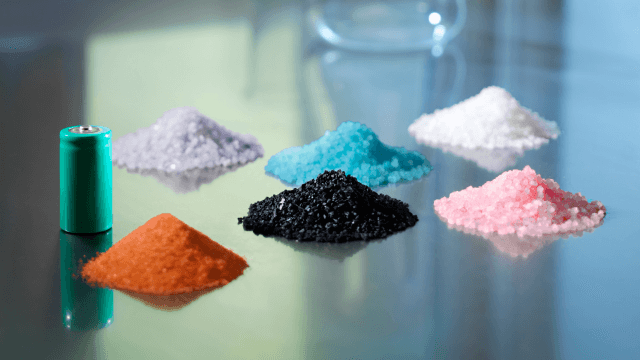
Accelerating circularity across the battery value chain
Alfa Laval’s heat transfer and separation technologies can be utilised across the entire battery value chain. These technologies accelerate circularity in refining, production and recycling processes. The broad offering of decanters centrifuges, disc-stack separators, evaporation systems and heat exchangers act as a valuable toolbox for true process improvement.
Below is an overview of the different segments of the battery value chain where you will find Alfa Laval’s industry leading solutions, helping to create more sustainable processes.
Mineral refining
The rapid growth in lithium-ion battery demand is putting pressure on the supply chains for critical raw materials like lithium. Efficient refining processes are essential to meet this demand sustainably than more traditional methods to meet the requirements and demands of current and future battery chemistries. Innovations such as direct lithium extraction (DLE) are being deployed to increase lithium recovery rates, reduce environmental impact, and ensure a stable supply of high-purity lithium hydroxide and lithium carbonate for battery production. Moreover, the battery industry's focus on reducing its carbon footprint and enhancing sustainability is a key driver for refining process improvements.
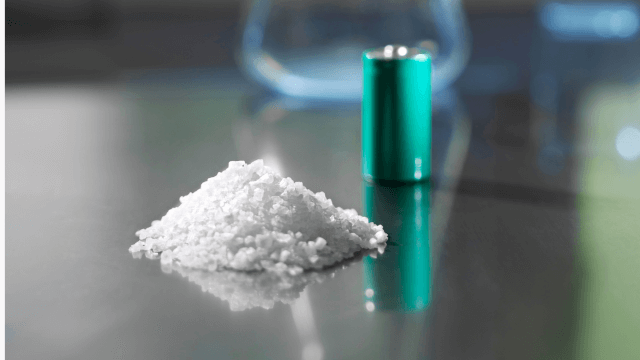
Battery and active material production
The International Energy Agency (IEA) projects that the global demand for lithium-ion batteries could reach up to 4,000 GWh by 2040. This growth is driven by government policies promoting sustainability, advancements in battery technology, and the increasing affordability of EVs. Additionally, the need for efficient energy storage solutions to balance the intermittent nature of renewable energy sources like solar and wind further fuels the demand for these batteries. To meet this growing demand, there is a pressing need for more efficient battery chemistries and production processes. Moreover, optimizing production processes to increase efficiency and reduce environmental impact is essential.
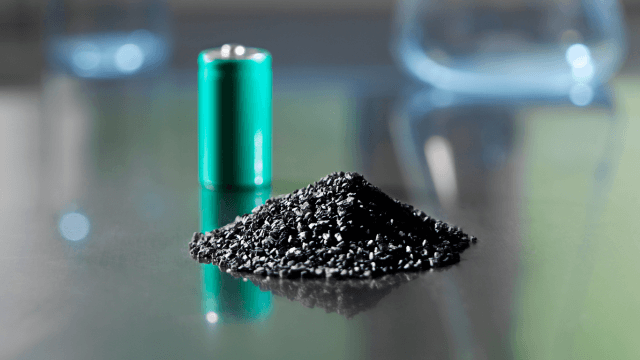
Battery recycling
The surge in demand for lithium-ion batteries raises concerns about the sustainability and availability of critical minerals like lithium, cobalt, and nickel. Recycling batteries helps mitigate the environmental impact of mining and reduces the reliance on finite natural resources. By recovering valuable materials from used batteries, recycling supports a circular economy and ensures a more sustainable supply chain for future battery production. Moreover, recycling lithium-ion batteries plays a crucial role in reducing greenhouse gas emissions associated with battery production. The IEA notes that recycling can significantly lower the demand for primary critical minerals, potentially reducing lithium and nickel demand by 25% and cobalt demand by 40% by 2050.
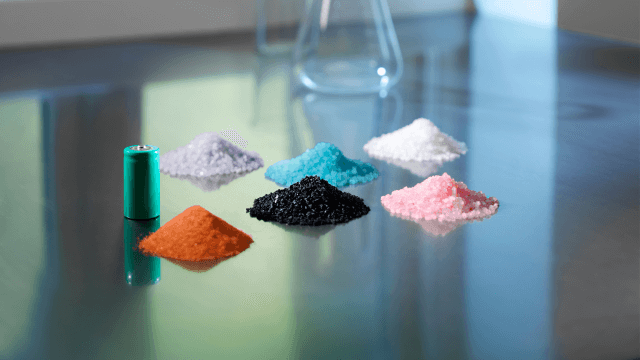
Process overview
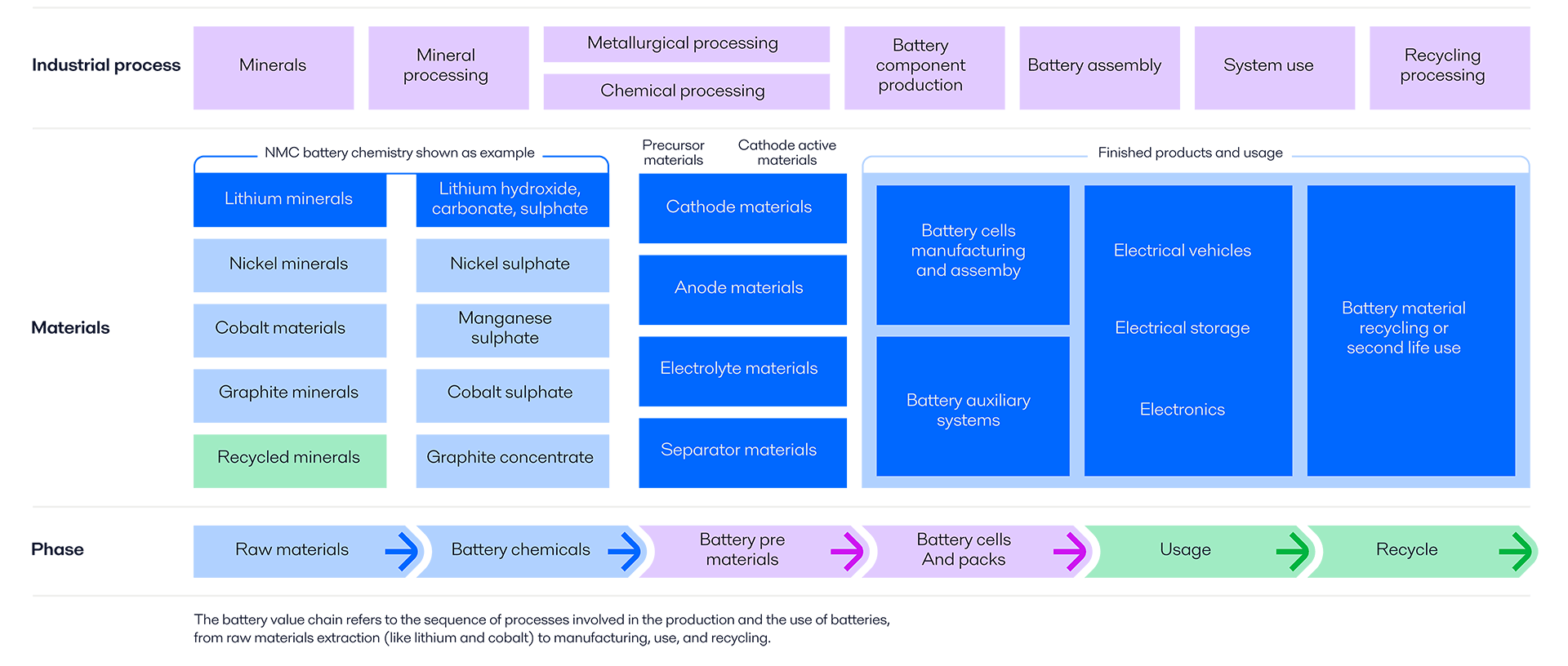